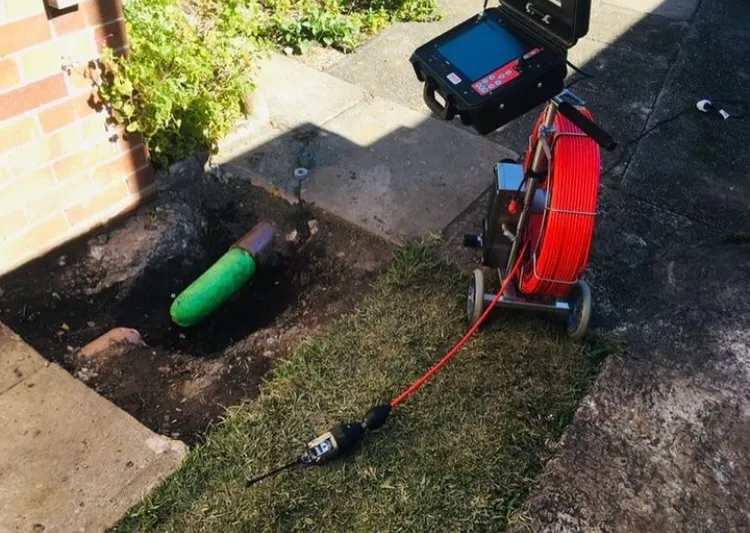
At Prime Pipe Relining, we specialise in offering state-of-the-art solutions to rehabilitate damaged and worn-out pipes. This guide is designed to educate homeowners, business owners, and industry professionals on the intricacies of pipe relining materials and the latest innovations enhancing the durability and functionality of relined pipes.
Pipe relining in Sydney, often regarded as a cost-effective alternative to traditional pipe replacement, involves inserting a new lining into existing pipes to repair damages such as cracks, leaks, and general wear. The process not only extends the life of the piping system but also minimises disruption to the surrounding environment. Understanding the properties of each material and the factors involved in selecting the right one for your specific needs is crucial for achieving optimal results. Join us as we explore these topics in depth, providing you with the knowledge to make informed decisions about pipe relining solutions.
What is Pipe Relining: Overview of the Process
Pipe relining is a modern, innovative, and non-invasive method to repair damaged, cracked, or leaking pipes without the need for extensive excavation. This technique is also known as Cured-In-Place Pipe (CIPP) lining. It offers a cost-effective and efficient solution for extending the life of existing piping systems, whether they are located beneath residential properties, commercial buildings, or municipal streets.
Understanding the Basics
Pipe relining essentially involves creating a new pipe within an old one. This is achieved by inserting a resin-saturated liner into the damaged pipe, which, once cured, hardens to form a new pipe that is robust, durable, and corrosion-resistant. This new pipe is seamless and jointless, reducing the risk of future leaks and blockages.
The Pipe Relining Process
The process of pipe relining can be broken down into several key steps, each crucial for ensuring the success and longevity of the repair.
Step 1: Initial Inspection and Assessment
The first step in the pipe relining process involves a thorough inspection of the existing pipe system using state-of-the-art CCTV camera equipment. This allows us to accurately identify the location and extent of the damage, understand the pipe layout, and determine the best relining strategy. This inspection is crucial for customising the approach according to the specific conditions of the pipe.
Step 2: Cleaning and Preparing the Pipe
Before the relining can begin, the existing pipe must be cleaned and prepared to ensure the liner adheres properly. This is typically done using high-pressure water jetting or mechanical cutting tools to remove any debris, roots, or blockages. The goal is to create a smooth surface inside the pipe for the liner to bond effectively.
Step 3: Measuring and Cutting the Liner
Based on the initial inspection, a liner made from a flexible felt material is cut to the precise length required. This liner is then impregnated with a specially formulated resin, which varies depending on the pipe material and the environmental conditions. The resin plays a crucial role as it will become the new pipe once cured.
Step 4: Inserting the Liner
The resin-saturated liner is then carefully inserted into the damaged pipe. There are various methods for this, including inversion (using water or air pressure to invert the liner into the pipe) or pull-in-place (pulling the liner into position with a cable). The choice of method depends largely on the pipe configuration and the extent of damage.
Step 5: Curing the Liner
Once the liner is in place, it needs to be cured to form the new pipe. This can be achieved through ambient curing, hot water, or steam, and in some cases, UV light. The curing process typically takes a few hours, after which the resin hardens and the liner becomes a solid, structural pipe within the old pipe.
Step 6: Post-Installation Inspection
After the liner has cured, another inspection is conducted. This final inspection ensures that the liner has adhered properly and that there are no gaps or misalignments in the newly created pipe. This step is essential for quality assurance and customer satisfaction.
Benefits of Pipe Relining
Choosing pipe relining over traditional pipe replacement methods offers numerous benefits:
- Minimised Disruption: The process is trenchless, meaning there is minimal digging and disruption to your property or daily operations.
- Cost-Effectiveness: As there is less excavation and manual labour involved, the overall cost can be significantly lower than traditional replacement.
- Longevity: The materials used in pipe relining are resistant to corrosion and can have a lifespan of up to 50 years.
- Eco-Friendly: Less excavation means a reduced environmental impact, with fewer disturbances to landscapes and ecosystems.
Exploring the Core Materials: From Epoxy to Vinyl Ester
Pipe relining is a crucial service we offer, providing a less invasive alternative to traditional pipe replacement. The choice of materials in this process affects everything from the durability of the repair to its environmental impact and cost-effectiveness. In this section, we’ll delve into the primary materials used in pipe relining, focusing on their properties, applications, and benefits.
Epoxy Resin
Characteristics and Benefits:
Epoxy resin is a thermosetting polymer commonly used in pipe relining. Known for its excellent mechanical properties and durability, epoxy forms a seamless, hard lining inside existing pipes. Once cured, it is incredibly resistant to chemical corrosion and can withstand high temperatures, making it ideal for both residential and industrial applications.
Application Process:
The epoxy is mixed and then poured into an inversion drum where it impregnates a felt liner. This liner is then inverted into the damaged pipe using water or air pressure. It moulds to the interior surface of the existing pipe, and then, through the use of steam or hot water, the epoxy is cured in place, forming a tight, structural bond with the pipe.
Longevity and Environmental Impact:
Epoxy liners are estimated to extend the life of a pipeline by up to 50 years. The material is also environmentally friendly as it does not leach harmful chemicals and reduces the need for extensive excavation, preserving the surrounding landscape.
Polyester Resin
Characteristics and Benefits:
Polyester resin is another thermosetting resin used in pipe relining. It is generally more cost-effective than epoxy and offers good resistance to a wide range of chemicals. Polyester resin is quicker to cure than epoxy, which can significantly reduce the time required for a relining job.
Application Process:
Similar to epoxy, polyester resin is used to saturate a felt or fibreglass liner before it is inserted into the pipe. The curing process may involve ambient curing without additional heat, or sometimes light heat, which accelerates the process.
Suitability:
It's particularly suited for sewer pipe relining because of its resistance to microbial-induced corrosion typically found in sewers. However, it is slightly less durable under extreme conditions compared to epoxy.
Vinyl Ester Resin
Characteristics and Benefits:
Vinyl ester resin offers a superior resistance to moisture and water, making it an excellent choice for relining pipes that are exposed to high levels of humidity and frequent water contact. It bridges the gap between polyester and epoxy, offering better chemical resistance than polyester and better cost-efficiency than epoxy.
Application Process:
The process for applying vinyl ester is similar to that of the other resins. It involves impregnating a flexible liner with the resin, inserting this liner into the pipe, and then curing it in place. Vinyl ester often requires careful handling due to its sensitivity before curing.
Best Use Cases:
This material is particularly beneficial in industrial settings where pipes may carry corrosive substances. Vinyl ester's resistance to acids, alkalis, and bleaches makes it a preferred choice for industrial wastewater systems and chemical processing plants.
Advanced Materials and Innovations in Pipe Relining
Pipe relining is a transformative approach to repairing damaged pipes without the need for extensive excavation. As professionals, we remain at the forefront of the industry by incorporating advanced materials and innovative techniques. This section explores the cutting-edge materials and technological advancements that have revolutionised pipe relining processes.
Epoxy Resin Liners
Composition and Properties:
Epoxy resin liners are favoured for their exceptional adhesive properties and durability. Composed primarily of epoxy compounds, these liners cure to form a seamless, jointless pipe within a pipe. The resin is chemically resistant to a wide array of substances, which makes it ideally suited for sewer and water pipes.
Application Techniques:
The installation involves the inversion of a resin-saturated felt liner into the existing pipe, which is then cured using ambient temperatures or assisted by hot water or steam. Ultraviolet (UV) light curing is another innovative method, providing a faster curing time and minimising disruption.
Silicate Resin Liners
Composition and Properties:
Silicate resins, another pioneering material in pipe relining, are known for their quick setting times and robust mechanical strength. These resins are typically composed of sodium silicates combined with various additives to enhance their properties.
Benefits:
This material is particularly effective in environments where heat resistance is necessary, and its rapid curing time allows for quicker project turnaround. Silicate resins are also an environmentally friendly option, with minimal volatile organic compound (VOC) emissions.
Cured-in-Place Pipe (CIPP) Technology
Technological Integration:
Cured-in-place pipe technology is a trenchless rehabilitation method that uses a textile liner tube and resin. Once cured, the liner forms a tight-fitting, corrosion-resistant new pipe within the damaged pipe. The use of CIPP has expanded rapidly due to its versatility and effectiveness in extending the life of infrastructure.
Advancements:
Recent advancements in CIPP technology include the use of fibre-reinforced liners, which provide increased strength and durability. Additionally, improvements in the curing process, such as LED-curing systems, have enhanced the efficiency of installations.
Glass-Reinforced Plastic (GRP) Liners
Composition and Advantages:
GRP liners are made from polyester resin and reinforced with glass fibre. This combination offers superior strength and durability, making GRP liners ideal for large diameter pipes and high-pressure environments.
Installation Process:
The installation of GRP liners is precise but straightforward, involving the winching of the liner into place and then using air or water pressure to expand it against the host pipe. Once in position, it is cured using UV light, resulting in a rigid, structural pipe that resists chemical attack and abrasion.
Robotics and Automation in Pipe Relining
Robotic Technology:
The integration of robotics in pipe relining has led to significant advancements in the precision and speed of repairs. Robotic cutters are used to remove obstructions and prepare pipes for relining, ensuring optimal adhesion and fit.
Automated Systems:
Automated curing systems have also improved the consistency and quality of liner installations. These systems control temperature and pressure during the curing process, leading to faster and more reliable outcomes.
Monitoring and Quality Assurance
Smart Sensing Technology:
To ensure the longevity and reliability of relined pipes, smart sensing technologies are being integrated. These systems monitor conditions within the pipes, such as pressure, flow, and even potential leaks, providing real-time data to maintain the integrity of the pipeline system.
Quality Control Techniques:
Advanced imaging and laser profiling tools are employed post-installation to verify the quality of the liner and adherence to specifications. This not only ensures compliance with industry standards but also guarantees customer satisfaction with every relined pipe.
Selecting the Right Material: Factors and Considerations
When it comes to pipe relining, selecting the right material is crucial for ensuring long-lasting and efficient repair. Our experience in the field has taught us that each situation calls for a different approach depending on various factors such as pipe condition, environmental impact, and budget constraints. Here’s a guide to help you understand the factors and considerations needed when selecting the appropriate material for pipe relining.
Understanding Pipe Conditions
1. Pipe Size and Diameter:
Different materials are better suited for different sizes and diameters of pipes. For instance, smaller or narrower pipes may benefit from the flexibility of certain cured-in-place pipe (CIPP) liners, while larger pipes might need more robust solutions like PVC or HDPE liners.
2. Pipe Material:
The existing material of the pipe (e.g., clay, concrete, metal, or PVC) can significantly influence the choice of relining material. Some materials adhere better to certain surfaces, and this compatibility can affect the longevity and effectiveness of the relining.
3. Current Pipe Damage:
The extent and type of damage (such as cracks, root intrusion, or corrosion) also play a critical role in material selection. Materials like epoxy are excellent for sealing and can handle minor cracks, whereas more extensive damage might require a structurally stronger solution like polyester resin.
Environmental and External Factors
1. Soil and Ground Conditions:
The surrounding environment where the pipes are laid impacts the choice of relining material. Factors such as soil type, moisture content, and the presence of aggressive chemicals in the soil can influence material degradation over time. For instance, epoxy resins often provide good resistance to chemical and environmental stress.
2. Temperature and Weather Conditions:
Pipe relining materials react differently to temperature changes. In Sydney, where the climate varies, materials must be chosen based on their ability to expand and contract without losing integrity. Polyester resins, for instance, perform well in a variety of weather conditions.
Durability and Longevity
1. Material Lifespan:
Each material comes with a different lifespan, and choosing a longer-lasting material might be more cost-effective in the long run. For example, epoxy and silicate resins are known for their durability, often lasting for several decades.
2. Wear and Tear Resistance:
The chosen material should be able to withstand everyday wear and tear along with specific challenges posed by the usage of the pipe. Materials that are resistant to abrasion and can handle high-pressure flows are preferable in commercial and industrial settings.
Compliance and Safety
1. Regulatory Compliance:
It’s essential to choose materials that comply with local and national standards. In Australia, materials used in pipe relining must meet specific Australian Standards to ensure safety and efficiency.
2. Impact on Water Quality:
For pipes carrying potable water, the relining material must not adversely affect water quality. Materials like CIPP liners are generally safe and meet the standards for water quality impact.
Cost-Effectiveness
1. Material Cost:
The cost of the relining material is a significant consideration. While higher-quality materials may have a higher upfront cost, their durability can lead to cost savings over time due to reduced maintenance and repair needs.
2. Installation Complexity:
Some materials require more complex installation processes, which can increase labour costs. Materials that are easier to install and cure may reduce overall project costs.
Conclusion
The field of pipe relining is both complex and fascinating, offering a range of solutions to extend the life and functionality of piping systems without the need for extensive excavation. Throughout this guide, we have explored the intricacies of the pipe relining process, starting with a comprehensive overview of how this method provides a cost-effective and efficient alternative to traditional pipe replacement. We discussed the core materials used in pipe relining, such as epoxy and vinyl ester, each offering unique benefits depending on the specific application. Our discussion also extended to advanced materials and recent innovations that are enhancing the durability and adaptability of relined pipes. Finally, we considered the critical factors necessary for selecting the right material for a given project, including environmental conditions, pipe usage, and budget constraints.